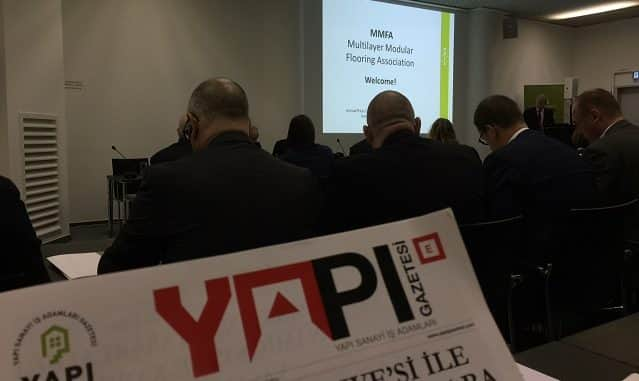
Product development in the multilayer segment is progressing at high speed. The growing choice of materials and types of build-up has made the market for MMF products extremely varied. The European MMFA Association is picking up this topic and will be presenting a special information area at the Domotex 2018: At the “Pier 12” in the centre of Hall 12, trade visitors can acquire a structured overview of the multilayer flooring product range.
MMFA President Matthias Windmöller: “The upturn of modular multilayer floorings and the appearance of new types of products has decisively changed the international flooring landscape in a short time. However, for the safety of retailers and flooring technicians and for the satisfaction of consumers, MMF floorings with reliable qualities should continue to dominate the market in the future. This is precisely what we in the MMFA are working for. “A steadily growing number of committed flooring manufacturers and suppliers are involved in the MMFA so that together they can help to shape the development of multilayer products actively and positively. With the new members Decoflooring GmbH (Troisdorf), Hymmen GmbH Maschinen- und Anlagenbau (Bielefeld), Proline Systems GmbH (Boppard) and Schoeller Technocell GmbH & Co. KG (Osnabrück), as of 1 January 2018 the association now has 22 ordinary members, 24 associate members and two sponsor members.
There are enough fields of work for the European industry network: In November 2017, following their major spring conference, the MMFA members met again for a further technical meeting to discuss the progress of the association’s paramount projects and to kick-start further measures. The primary tasks of the association include the topic of “Product clustering”, as MMFA Technical Workgroup Convenor Volker Kettler explained: “Our MMFA experts have once again reviewed the MMF product system, which categorises the multilayer flooring with their different build-ups in logical groups according to their individual specifications. This has produced further refinements. Class 1 now includes cork top-layers, and Class 2 is split up in 2A and 2B. Based on this “product cluster”, the intention is that buyers and installers can then clearly identify typical requirements for the respective product, e.g. “important necessities for laying” (see information box below for details).
Implementing pragmatic quality standards
Future-proof solutions are also in demand in the area of international standardisation work. In this context, in 2017 the MMFA was able to intensify contacts with the new US American industry association, the MFA, through mutual invitations. Both industry associations want to develop their technical cooperation still further in the future. Volker Kettler: “From the outset, the MMFA’s creed was to be open to innovations. In view of the many new mixed products, rules must be created early, which ensure clarity, transparency and above all safety for customers. That is why we are actively involved in the implementation of pragmatic quality standards on all markets and support sustainability considerations in the industry.”
The MMFA promotes continuous development of the product standards. It has thus submitted an application for an addition to the EN 16511, into which new findings from the association’s own research has been incorporated. The proposals include a) the introduction of tests with the “large ball” (impact resistance test) and measurement of scratches on the surface layer only; b) deleting “Method B” (visual comparison before and after the test) from the testing of microscratch resistance and c) performance of the “castor chair test” without underlay material.
The MMFA has already carried out valuable pioneering work on the development of new parameters for testing the joint strength and the temperature resistance of MMF boards. The association is currently progressing well with the topic of “top surface localised heat conditions (hot spots)”: Test series within the scope of the EU-funded “hot spot” research product have been underway in the IHD Institute for Wood Technology in Dresden and individual member firms for some time now. The objective of this project is to work up new, practical test methods for multilayer modular floorings for floating installation. Various click systems and different underlay materials are being considered.
According to the MMFA extrapolation for 2017, the upward trend of modular multilayer floorings continues. According to the MMFA forecast, annual increase rates of 10 to 15 % are also possible in the overall MMF market in the next three years. In Central Europe the floorings in the MMFA Class 1, i.e. products based on wood-based panels (HDF) continue to determine the market: In 2017, the MMFA manufacturers in this class accounted for over 80 % of sales in Germany, Austria and Switzerland alone, and a further 14% in the other West European states. “In 2017, our members in the MMFA Class 1 may have broken through the ten million square metres mark for the first time ever”, MMFA Chairman and Marketing Workshop Convenor Sebastian Wendel was pleased to say.
The MMFA also registered annually increasing sales figures for MMFA Class 2 products (polymer or polymer-composite substrate with polymer surface layer and/or lacquer). However, due to the growth in members, more producers are now reporting their quantities in Class 2. Compared to Class 1, the regional distribution in Class 2 looks rather different: On the more than 50 million m2, which were sold worldwide by the members in 2017 according to the MMFA extrapolation, around 23 million m2 were sold in North America and almost 22 million m2 in West Europe. In West Europe the MMFA members thus accounted for an almost 40% share of the total market for Class 2 products in – and the trend continues to rise. In the MMFA Class 3 (all other build-ups, which do not fall under Class 1 or 2 or external standards – e.g. organic wear layers or mineral core materials), due to cartel law provisions that affect at least five reporting firms, no data can be published for 2017.
Plenty of variety on the floor
Modular multilayer floorings not only combine the advantageous product characteristics of different types of floors in one product – they can also score points with their enormous up-to-date design selection. Synchronous embossed decors with matt surfaces and a pleasantly soft touch are all the rage in the MMF segment. The shabby chic look continues to be popular in the MMF segment. These also include replica “signs of wear and tear” such as scratches in the surface of the MMF boards. In the wood reproductions matt white and grey hues are once again increasing in significance. The many varieties of oak continue to reign supreme, yet the new decors based on acacia, pine, alder or walnut wood are also appealing. New stone looks in the MMF collections extend the possibilities of creative room design. While in the non-housing segment, modern concrete look variants are frequently used, in the housing segment and increasing number of customers are opting for contemporary interpretations of classics such as slate, granite, sandstone, as well as ornamental marble decors. All-round chamfers and structures typical of stone that you can really feel supplement the high-quality look and feel of these MMF floorings.
The abundance of product build-up variants is growing and opens up diverse possible uses for MMF floorings. Sustainable material combinations continue to increase in importance in this segment: Numerous brand manufacturers now completely abstain from the use of phthalates or PVC and instead use eco-plasticisers such as vegetable oil-based epoxides or polymers from the polyolefins group.
New arrivals on the market are thin MMF constructions based on sheet goods with a material thickness of only four to five millimetres for floating laying with click profile. In several products, wood-based highly compacted and double-sealed cores are used. These “Ultra Wood Fibre Boards” (UWF) promise high form stability, even when large temperature fluctuations occur. A further variant in the product build-up contains natural, mineral-based core materials. Equally, polymer products without wood fractions in which, for example, a glass fibre stabilisation layer is incorpoarated in the core, are also offered: This allows the individual elements to achieve high form stability even if subjected to climate fluctuations.
Moisture protection and self-repair
MMF polymer floorings with anti-swell cores and solid polymer materials are predestined for use in damp and wet rooms. Thanks to modern click systems they can be laid effortlessly and precisely. Unwanted joints are prevented by the high jointing stability and pull-out strength of the systems. The innovative solutions of the multi-layer manufacturers also include surfaces with a self-repair function: In case of surface deformations, for example, the indentations that can be caused by furniture feet, the molecules “remember” their initial position and move back there in a very short time when no longer loaded.
Well-coordinated overall systems help to optimise the properties of the modular multilayer floorings. Here innovative beading, profile and underlay developments come to the fore. For example, the underlay manufacturers have developed dimensionally stable and pressure-resistant products for the special requirements of the MMF floorings. Laying is made easier by format optimisations, several of the new underlays also have improved slip-brakes.
The development work of the manufacturers continues and more exciting innovations for modular multilayer floorings are also to be expected in 2018. The MMFA members are very well positioned here and will deliver solutions for new aha effects on the floor.