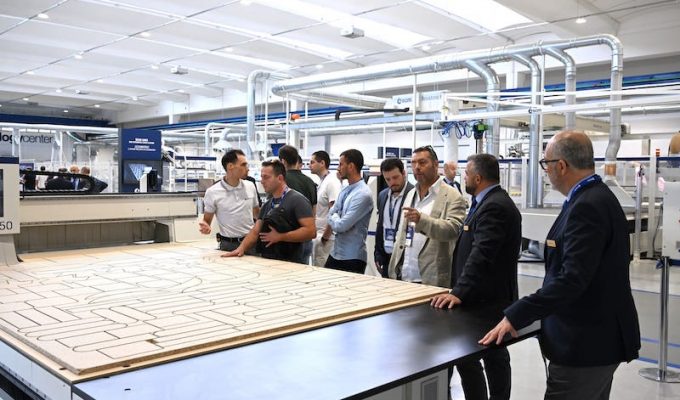
SCM presents two new CNC machining centres to enhance and integrate its range for nesting processing: “morbidelli x50” and “morbidelli x100”.
The new nesting frontiers start in Rimini. It is here, at SCM’s Headquarters, that two new CNC machining centres were presented on the 13 and 14 September for the sector: “morbidelli x50” and “morbidelli x100”.
The two solutions further enhance and integrate the “morbidelli x” range already chosen by leading market clients thanks to its capacity to apply high speed and maximum flexibility to nesting machining to meet a market demand that is increasingly focused on “batch one”.
SCM has once again shown, with these new CNC machining centres, its ability to transfer high performance even onto “entry level” solutions, guaranteeing a number of advantages which differentiate its nesting range at highly competitive prices. Every detail has been scrupulously designed with a view to making all the necessary features accessible from an efficiency, machining quality and predictive maintenance point of view.
From a software point of view, it not only has the new Maestro Lab intuitive and dynamic CAD/CAM design system, for programming both from the office and machine, but “morbidelli x50” and “morbidelli x100” also have a state-of-the-art SCM Smart cut algorithm. Elimination of both unproductive times and waste and a reduction in energy consumption and material scraps are the main advantages of this optimiser which proves ideal for the nesting cut of even the smallest pieces. SCM Smart cut applies sequences and cutting technologies which, without affecting either the speed or arrangement of the pieces in the program, improve the finishing quality and reduce cycle times.
Highlighted for both machining centres, we also find the SMS – Spoilboard Management System software, an advanced solution which, thanks to an exact calculation carried out on the machine, makes it easier for the operator to manage the spoil panel signalling pro-actively when it needs to be rectified or replaced.
Important innovations can also be found in the mechanical characteristics.
One example is the worktable with High Grip Vacuum technology on the “morbidelli x50”: practical and sturdy, it is the only one of its kind to guarantee the best grip on the piece thanks to an exclusive SCM patented deflector which distributes the vacuum across the whole surface thus maximising the grip even in the case of panels that are smaller than the machine’s overall area.
Another significant advantage of “morbidelli x50” is its flexibility thanks to XS Device, a device that makes it easier for the operator to refer and machine all the pieces directly on the spoil panel, even the smallest ones.
Also taking priority of place is the SAFE – Safe Advanced Fixed Equipment protection system, one of a kind on the market for ensuring maximum operator safety at all times. This occurs thanks to a perimeter photocell system which provides free access to all four sides to machine right across the board.
The advantages of “morbidelli x50” are rounded off with the top performances of the drilling units, with 8000 rpm RO.AX technology, and boring units capable of machining in nesting up to 40 metres per minute.
The innovation at the heart of SCM’s new machining centres for nesting is further amplified with “morbidelli x100”.
Some of the advantages being highlighted include its excellent configuration versatility: the model is available in different versions, from stand-alone machine to integrated cell with automatic “flexstore” warehouse, right up to the “push” and “mat” versions respectively fitted with automatic pusher and motorised unloading belt to simplify and speed up the exit of the pieces in complete safety and, in this latter case, even without manual interventions.
SCM is, therefore, capable of offering the most suitable solution to the client irrespective of their investment abilities.
Another distinctive feature is the maximum grip on the piece guaranteed by Smart vacuum, the system which concentrates the vacuum only in the parts still to be machined, thus avoiding dispersion in the areas already nested. An innovation that has been added to an already high-performing worktable with PHE – Phenolic High Efficiency technology especially designed for use with the spoil panel.
Not just nesting: the other new entries for “accord”
CNC machining centres dedicated to the furniture industry
The event held on 13-14 September in Rimini was also an opportunity to present the latest new entries in the range of “accord” CNC machining centres.
Three years after the launch of “accord 500” and “accord 600”, solutions which have dramatically changed the rules of play in the production of doors, windows, staircases and solid-wood elements, SCM is presenting new finishing upgrades to the range, for machining the panel and the furniture world, but always “According to wood”, starting from the intrinsic peculiarities of the material machined and the client’s most pressing demands.
The strong points of this range which has conquered leading clients at international level, remain unvaried such as the dual motorised “gantry” structure, the 5-axis operator unit with excellent performance, the innovative suction systems to guarantee maximum cleaning of the machine and the surrounding environment, the high-capacity tool magazines with Maestro power TMS intelligent management system and the CAD/CAM Maestro Lab software for designing and programming.
The latest new entries from SCM regarding:
“Optizone” patented system connected to the Maestro Lab software is revolutionising the CNC bar machining centres: with a simple click, the size of the two work areas can be defined as early as the programming stage, based on the pieces to be machined. This function is also available for the clamps.
New SVP – Single Vacuum Pods function to independently secure the pieces on each semi-table: it is possible to have several separate vacuum areas, and the pieces can be loaded onto the machine by activating one suction unit at a time. This allows for excellent management of the scraps.
The two functions mentioned, developed to deal with the vacuum, are particularly useful in the case of asymmetrical machining areas.
Increase in the length of the 1900 y-axis work surface compared to the current 1600 y-axis to carry out horizontal machining more effectively and simply inside the pieces blocked with clamps with the 5-axis electrospindle.
Greater configurability of the operator unit with new boring and drilling heads and new multifunction units.
New chain tool magazine, Quadro 35, positioned on the rear side of the mobile gantry-type structure, ideal for those always needing numerous tool positions easily and rapidly to hand in a reduced space.
As Bruno Di Napoli, Business Unit Manager for SCM’s machining and drilling centres explains: “Once again leading all the developments in these new solutions is the will of the company to place the client and their experience in using the machine at the centre of everything.
Whether we are dealing with aspects of software programming, digital connectivity or ergonomics and ease of use, we aim to ensure the operator always works under maximum safety conditions without compromising in any way on practicality and production efficiency”.
Scm Group is a global leader in technologies for machining a wide range of materials and industrial components. Across the globe, the group’s companies act as highly reliable partners to leading industries in a wide range of product sectors, from furniture to construction, automotive to aerospace, and yachting to plastic machining.
Scm Group coordinates, supports and develops a system of industrial excellence in 3 large highly specialised production centres in Italy, with a turnover of 900 million Euro, with 4,000 employees and a direct presence on all 5 continents.